Mastering CMP: Precision in Microelectronics
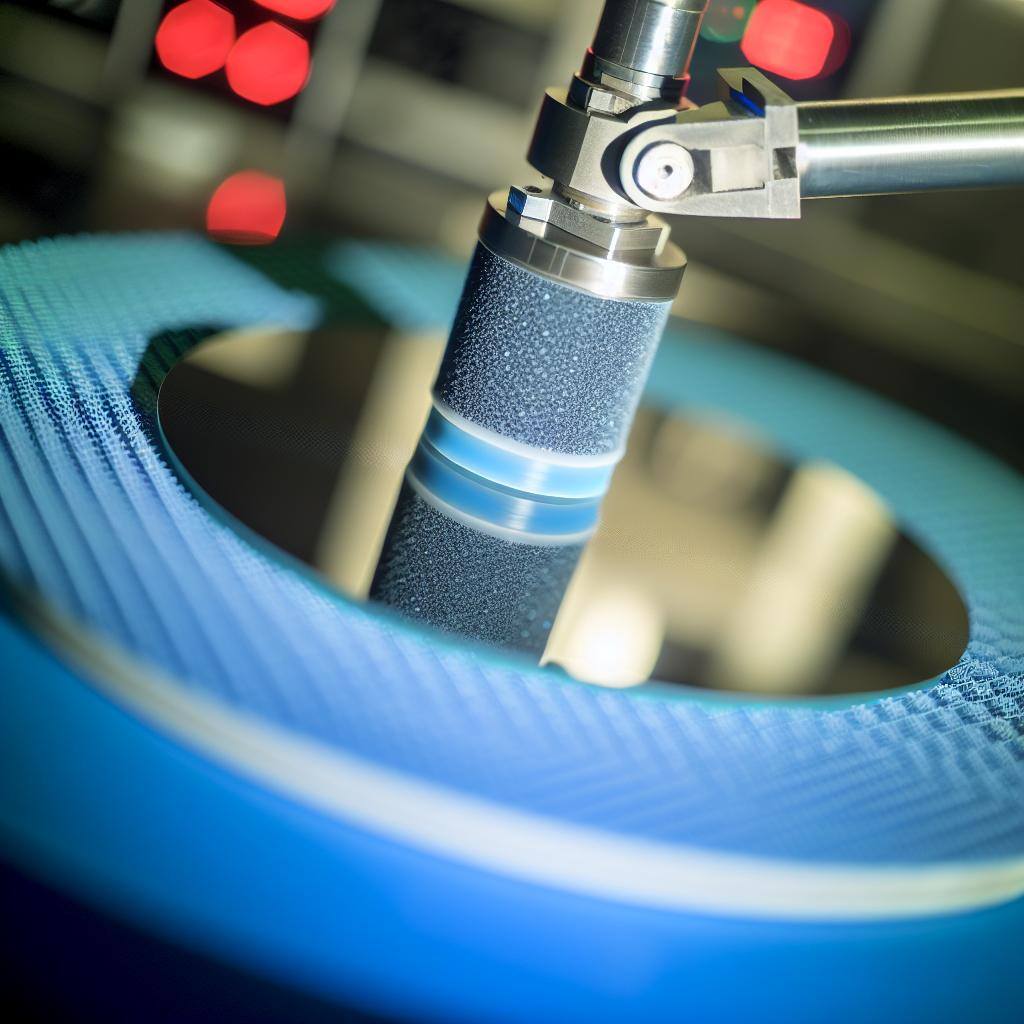
Explore the CMP(Chemical Mechanical Polishing) process and how it contributes to the manufacturing process of semiconductor devices.
Understanding CMP in Microelectronics
Chemical mechanical polishing (CMP) is a crucial process in the field of microelectronics. It involves the simultaneous application of chemical and mechanical forces to remove material from the surface of a semiconductor wafer or other electronic components. CMP is used to achieve a high level of planarity and smoothness, which is essential for the fabrication of advanced microelectronic devices.
The CMP process begins with the application of a chemical slurry that contains abrasive particles. These particles help in the removal of unwanted material from the wafer surface. Simultaneously, a polishing pad or disk applies mechanical pressure to the wafer, ensuring uniform material removal. The combination of chemical and mechanical forces enables precise control over the removal rate and surface quality.
Understanding the various aspects of CMP is crucial for mastering the precision required in microelectronics. By studying the interaction between the chemical slurry, abrasive particles, polishing pad, and the surface of the wafer, engineers can optimize the CMP process to achieve the desired level of planarity and smoothness.
Key Components of the CMP Process
To achieve precision in microelectronics, it is important to understand the key components of the CMP process. These components include:
- Chemical Slurry: The chemical slurry is a mixture of abrasive particles and chemical agents. It plays a crucial role in material removal and surface polishing.
- Polishing Pad: The polishing pad is a critical component that applies mechanical pressure to the wafer surface. It must be carefully designed to ensure uniform polishing and prevent defects.
- Carrier: The carrier holds the wafer during the CMP process and provides a stable platform for polishing. It must be compatible with the polishing pad and provide sufficient pressure control.
- Slurry Delivery System: The slurry delivery system is responsible for delivering the chemical slurry to the polishing pad. It must maintain a consistent flow rate and distribution for optimal CMP performance.
- Monitoring and Control Systems: Monitoring and control systems are used to measure and adjust various parameters during the CMP process. These systems help in optimizing material removal rate, surface quality, and overall process performance.
Challenges and Solutions in CMP
While CMP is an essential process in microelectronics, it comes with its own set of challenges. Some of the common challenges faced in CMP include:
- Selectivity: Achieving selective material removal can be challenging, especially when dealing with multiple layers of different materials.
- Planarity: Maintaining a high level of planarity across the entire wafer surface is crucial for the successful fabrication of microelectronic devices.
- Defects: CMP can introduce defects such as scratches, dishing, and erosion. Minimizing these defects is essential for achieving precision in microelectronics.
To overcome these challenges, engineers have developed various solutions. These include the use of advanced slurry formulations, innovative polishing pad designs, optimized process parameters, and advanced monitoring and control systems. By continuously improving these solutions, the CMP process has evolved to meet the ever-increasing demands of the microelectronics industry.
Atomic Layer Deposition, Metal Deposition, and Chemical Mechanical Polishing
Metallization, in the context of semiconductor manufacturing, refers to the process of depositing metal layers onto a substrate, typically silicon. These metal layers are used for various purposes, including interconnecting different components on the chip.
ALD (Atomic Layer Deposition) is a thin film deposition technique that allows for precise control over film thickness and composition at the atomic level. It involves depositing thin layers of material onto a substrate by sequentially exposing the substrate to different precursor gases in a cyclic process.
The combination of CMP and ALD can be used in semiconductor manufacturing for planarization. CMP can be used to planarize the surface of a substrate after metal deposition by ALD, ensuring uniform thickness and reducing surface roughness.
Overall, the combination of CMP and ALD plays a crucial role in achieving high-performance and reliable semiconductor devices by enabling precise control over the thickness, composition, and topography of metal layers.