Understanding the Principles of DIC Microscopy
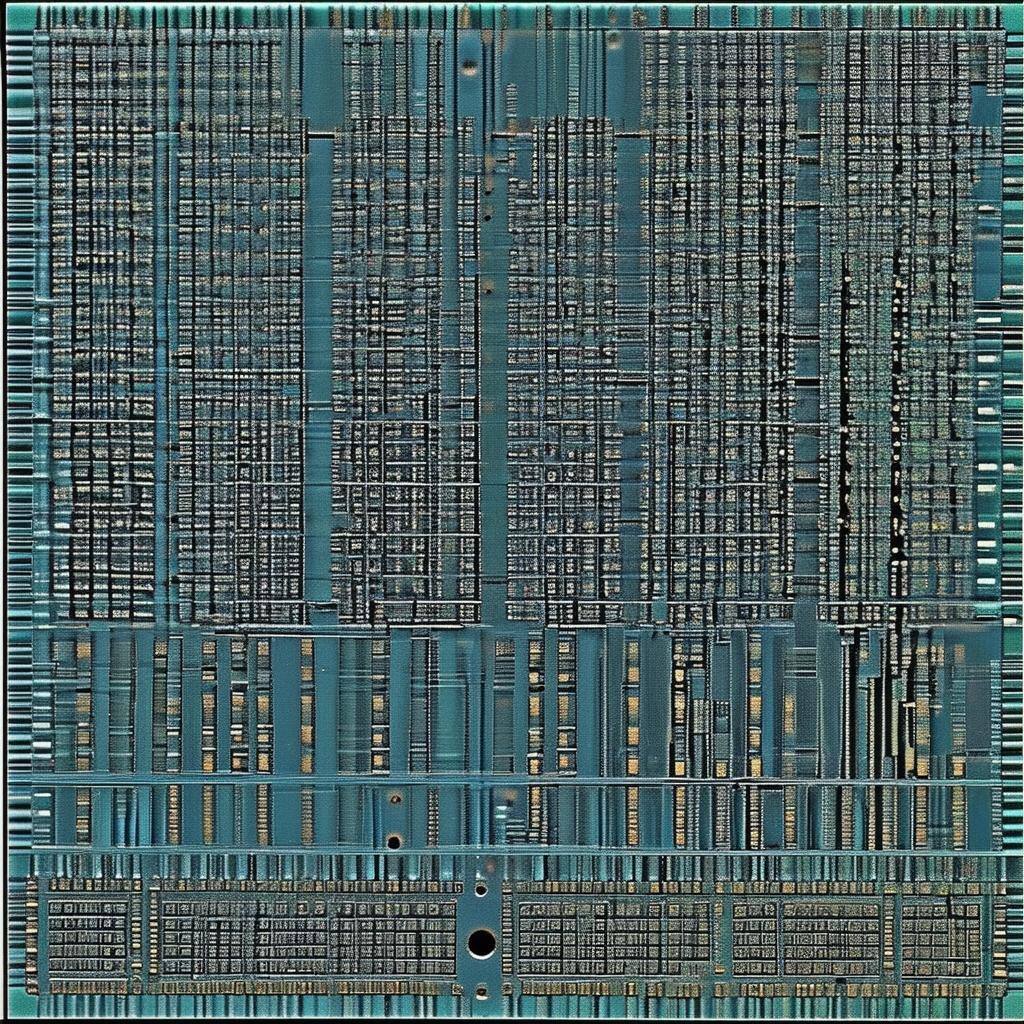
Jerzy Nomarski, a Polish scientist born in the southern part of Poland, participated in resistance efforts against the Nazis during World War II and was later captured by the Nazi forces. Near the end of the war, as his homeland fell under Soviet occupation, he fled to Belgium in pursuit of freedom. Although he is known by the name Georges, his name in Polish is Jerzy.
The Basics of DIC Microscopy
Nomarski Microscopy, also known as Differential Interference Contrast Microscopy, was developed by Jerzy Nomarski. This technique is effectively utilized in natural sciences and semiconductor manufacturing. It creates contrast in transparent objects and uses polarization phenomena to apply false color, aiding in the examination of the three-dimensionality of objects.
By using polarized light and Nomarski prisms, DIC Microscopy can convert phase differences in light passing through a specimen into differences in intensity, producing a high-contrast image with a pseudo-3D effect.
This technique is particularly useful for observing live cells, thin tissue slices, and other transparent specimens where traditional staining methods might not be applicable. With DIC Microscopy, researchers can visualize detailed structures and subtle differences in optical density without altering or damaging the sample.
How DIC Microscopy Enhances Manufacturing Processes
In the manufacturing industry, particularly in semiconductor production, quality control is paramount. DIC Microscopy provides a non-destructive method to inspect materials and components with high precision. By enabling the visualization of minute surface variations and defects, DIC Microscopy helps in identifying potential issues early in the manufacturing process.
For example, when using an electron beam (E-beam) for imaging photoresist, there is a significant issue of shrinkage that can occur. This shrinkage can lead to inaccuracies in the lithography process, affecting the quality and precision of the results. Additionally, there is the problem of charging, where the accumulation of electrical charge on the surface of the photoresist can distort the image and complicate the imaging process.
These challenges make it difficult to use high-resolution, high-energy electron microscopy effectively for such purposes. Therefore, in the evaluation of photomasks, techniques that utilize light, such as Nomarski Microscopy, are employed. This method, along with its associated failure analysis and inspection technologies, provides a more suitable alternative. By leveraging the capabilities of Nomarski Microscopy, early detection of potential issues is possible, allowing for timely interventions. This proactive approach significantly reduces the risk of producing defective products, ensuring higher quality and reliability in the manufacturing process.
Nomarski microscopy detects partially developed photoresist on the semiconductor wafer.
Light Path in DIC Microscopy
- Unpolarized light enters the microscope and is polarized at a 45° angle.
- The polarized light passes through the first Nomarski-modified Wollaston prism, where it is split into two rays polarized at 90° to each other, known as the sampling and reference rays.
- The condenser focuses the two rays for passage through the sample, ensuring they pass through two adjacent points in the sample, approximately 0.2 μm apart.
The sample is illuminated by two coherent light sources, one polarized at 0° and the other at 90°. These illuminations are slightly misaligned, with one being slightly offset from the other.
The path of light through a DIC microscope. The two light beams should remain parallel between the condenser and objective. - The rays traverse adjacent areas of the sample, separated by the shear. This separation is typically similar to the microscope's resolution. They encounter different optical path lengths where the areas vary in refractive index or thickness, causing a phase shift in one ray relative to the other due to the delay in the more optically dense material.
As many pairs of rays pass through adjacent points in the sample (and are absorbed, refracted, and scattered by the sample), an image of the sample is carried by both the 0° and 90° polarized light. Viewed individually, these would be bright field images of the sample, slightly offset from each other. The light also carries phase information, invisible to the human eye, which is crucial later. The different polarizations prevent interference between these two images at this stage. - The rays pass through the objective lens and are focused for the second Nomarski-modified Wollaston prism.
- The second prism recombines the two rays into one polarized at 135°. The combination of the rays results in interference, brightening or darkening the image at that point based on the optical path difference.
This prism overlays the two bright field images and aligns their polarizations to allow interference. However, the images do not perfectly align due to the offset in illumination—this means interference occurs between rays of light that passed through adjacent points, which have slightly different phases. The phase difference, due to the optical path length difference, results in "optical differentiation" of the optical path length, creating the observed image.
For more detailed information on imaging techniques, please refer to Wikipedia.
https://en.wikipedia.org/wiki/Differential_interference_contrast_microscopy
Optimizing Photoresist Inspection with DIC Microscopy
Photoresist inspection is a critical step in semiconductor manufacturing, as it directly impacts the quality and functionality of the final product. The photoresist layer acts as a stencil for etching patterns onto semiconductor wafers, which are essential for creating the complex circuits found in electronic devices. Any defects in this layer can lead to significant issues in the subsequent manufacturing stages, potentially resulting in costly rework or even complete product failure.
DIC Microscopy enhances this inspection process by providing exceptionally clear, high-contrast images of photoresist patterns. This advanced imaging technique allows for the precise detection of a wide range of defects, such as undercutting, where the photoresist is eroded more than intended, leading to unwanted material removal. It also identifies over-deposition, where excess photoresist material accumulates, potentially causing short circuits or other malfunctions. Additionally, DIC Microscopy can reveal irregularities in pattern edges, which might otherwise go unnoticed but can significantly affect the performance and reliability of the semiconductor device.
By utilizing DIC Microscopy, manufacturers can ensure that photoresist layers are correctly applied and developed, leading to more accurate pattern transfer onto the semiconductor substrate. This optimization is vital for the production of high-performance semiconductor devices, where even minor deviations can lead to significant performance issues, such as increased power consumption, reduced processing speed, or complete device failure. Ensuring the integrity of the photoresist layer through meticulous inspection with DIC Microscopy not only enhances the quality of the final product but also contributes to the overall efficiency and cost-effectiveness of the manufacturing process.
Utilizing Deep Block for Photoresist Evaluation
By incorporating computer vision and tools like DeepBlock into the inspection process, image segmentation can be significantly improved, enabling more efficient and accurate defect detection. Deep Block is an AI-powered tool designed to simplify the creation and deployment of machine learning models without requiring extensive programming expertise. It allows users to process large datasets and develop customized pipelines for specific use cases, such as identifying and segmenting defects in photoresist layers captured by Nomarski microscopy. This integration makes it possible to automatically detect and highlight irregularities or contamination zones, reducing the reliance on manual inspection.
The combination of computer vision and tools like Deep Block brings significant value to the inspection of photoresist layers. First, it automates the defect detection process, reducing the time and effort required for manual inspection while increasing throughput. Second, the use of machine learning models enhances accuracy by identifying minute defects or anomalies that human inspectors might miss. This level of precision ensures consistent results and eliminates the variability associated with human judgment, such as fatigue or subjective decision-making.
Another advantage is scalability, as AI-powered tools can handle a large volume of images, making them ideal for high-throughput manufacturing environments especially assessing large area DIC microscopy. Analyzing large-area images is a complex task that cannot be quickly handled by AWS or simple computer vision software, nor by companies providing inspection equipment.
This complexity arises from the need to process vast amounts of data with high precision and accuracy, which often exceeds the capabilities of standard solutions. For more detailed information on this topic, you can refer to deepblock.net/resources. Moreover, by utilizing Deep Block, users can create and deploy a wide range of AI models for detecting photoresist or other structures without the need for coding. This powerful advantage extends beyond DIC micrographs to include Scanning Electron Microscopy (SEM) and Transmission Electron Microscopy (TEM) images as well. This flexibility allows users to tailor their inspection processes to various imaging techniques, enhancing the versatility and effectiveness of their analysis.
A standard workflow utilizing these technologies starts with obtaining high-quality Nomarski microscopy images of photoresist layers. These images undergo preprocessing to improve their quality, which includes using the annotation tool from deepblock.net to create a training dataset for automation. For guidance on getting started with DeepBlock, visit the following link: https://www.deepblock.net/product/manual
Using DeepBlock, machine learning models can be trained to segment and identify specific defects or irregular patterns in the images. The system then quantifies the defects and provides actionable insights to manufacturing teams. This feedback can be integrated into production systems, enabling proactive measures to prevent recurring defects and improve overall product quality.