Impact of Ligament Structures on MLCC Electrode Performance and Reliability
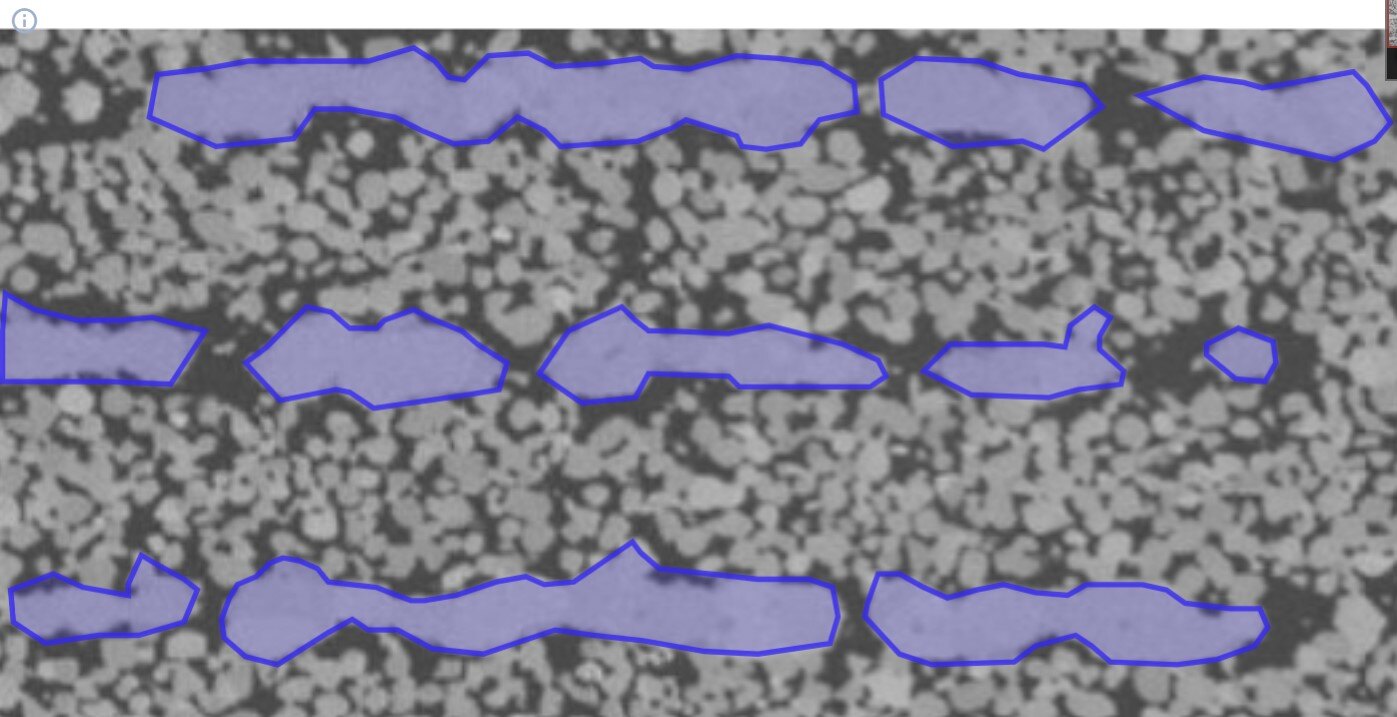
Discover how the intricate ligament structures within MLCC electrodes significantly impact performance and reliability in electronics manufacturing.
Understanding Ni Ligament Structures in MLCC Electrodes
Multi-layer ceramic capacitors (MLCCs) are renowned for their exceptional high volumetric efficiency, which allows them to store a large amount of electrical charge in a relatively small volume.
This characteristic is particularly advantageous in the electronic devices, where space is at a premium.
Additionally, MLCCs are celebrated for their reliability, ensuring consistent performance over extended periods, which is crucial for maintaining the functionality of electronic systems. Their excellent high-frequency characteristics make them ideal for applications that require rapid signal processing, further solidifying their strong position in the competitive ceramic capacitor market.
As modern electronic devices continue to shrink in size, the demand for components that can deliver high performance in compact forms has intensified.
Consequently, the thickness of internal electrodes and dielectric layers within MLCCs is being progressively reduced, thereby enhancing their volumetric efficiency.
The latest MLCC chips are typically composed of alternating layers of nickel (Ni) electrodes and barium titanate (BaTiO3 or BT) dielectric layers.
The BT sheets are fabricated through a process known as tape casting, which involves creating a slurry with BT powder.
Meanwhile, the electrodes are crafted by screen printing a paste that contains Ni particles and nano-sized barium titanate additives onto the dried BT sheets.
These nanoparticles play a critical role in minimizing the sintering shrinkage mismatch between the Ni and BT layers, which is essential for maintaining structural integrity.
Once the organic binder is removed, the chips undergo a sintering process in a reducing atmosphere. To achieve even higher performance levels in MLCCs, the thin films are being made increasingly thinner, a development that, while beneficial, also heightens the risk of defects and presents technical challenges.
In industrial base metal electrode MLCCs (BME-MLCCs), where layer thicknesses are about 1 micron or less, discontinuities in the electrodes have been observed.
For instance, during the sintering of Ni-MLCCs, a thin liquid alloy layer, approximately 10 nanometers thick, composed of nickel, barium, and titanium, forms at the Ni/BaTiO3 interface.
The presence of this high-temperature interfacial liquid film alters the interfacial free energy and provides a rapid kinetic pathway for material transport, which can accelerate Ni particle growth and lead to electrode degradation. Understanding and controlling these processes are vital for enhancing the performance and reliability of MLCCs.
Electrode Stability, Microstructural Optimization, and Sintering Processing
MLCCs with nickel (Ni) electrodes and barium titanate (BaTiO3) dielectrics face stability challenges due to the mismatch in mechanical properties and layer thickness. Ni electrodes have a higher elastic modulus than BaTiO3, while the dielectric layer is thicker than the electrode layer. This disparity leads to mechanical stress during thermal processing.
Ni electrodes contract significantly at temperatures between 500°C and 1000°C. Since the contraction of the electrodes outpaces that of the dielectric layer, tensile stress arises in the electrodes due to deformation rate differences.
Stress-induced diffusion exacerbates roughness in the electrode layer, forming discontinuities that negatively impact performance. Rapid heating during processing can mitigate these issues by kinetically suppressing the formation of the interfacial liquid layer. This approach reduces temperature-dependent capacitance variations, minimizes BaTiO3 particle size, and enhances electrode continuity, thereby improving the MLCC lifespan.
Maintaining smoother and more continuous electrodes is critical for MLCC performance. The capacitance of MLCCs depends on the continuity and connectivity of the electrode area, and discontinuities lead to capacitance loss. Lifespan is further limited by the degradation of insulation resistance in DC electric fields, a process accelerated at higher temperatures.
Electrode roughness influences the local electric field and dielectric layer thickness. Preventing sharp intrusions of electrodes into the dielectric is essential for minimizing device failure. Additionally, the design of ligament structures in electrodes plays a vital role in electrical performance. By optimizing the ligament network, manufacturers can improve conductivity, dielectric strength, and energy efficiency.
These advancements result in MLCCs that perform reliably under demanding conditions, such as high-frequency and high-temperature environments. Precision engineering of ligament structures ensures that modern MLCCs meet stringent requirements, supporting the needs of advanced electronic devices.
Degree of Discontinuity
To assess the quality of MLCC chips, scientists and engineers utilize a metric called the Degree of Discontinuity (D). This metric is defined as follows:
D = Ld/L0
Where:
L0: The total length of the observed metal layer
Ld: The integrated length intersecting with pores or defects within the observed region
A lower D value suggests that the internal metal layer of the MLCC is more continuous and has fewer defects, indicating higher quality. Consequently, the D value is a crucial indicator for evaluating MLCC quality.
MLCC manufacturers strive to improve product quality and assess process efficiency by using the D value as a key management metric. To decrease D, manufacturers can focus on enhancing the microstructure of the electrodes or developing methods to minimize defects during the sintering process.
The length of Ni ligament structures within MLCC electrodes is a critical factor in determining capacitance. Longer ligaments can offer a greater surface area for charge storage, thereby increasing the device's capacitance.
Automated calculation of the Degree of Discontinuity using Deep Block and its semantic segmentation AI tool
The Role of Ni Electrode Roughness in MLCC Quality
The shape of Ni electrodes, in addition to their size, plays a critical role in evaluating the performance of MLCCs.
The roughness of nickel (Ni) electrodes significantly affects the quality and performance of the device. Below is a detailed explanation of this relationship:
1. Effects of Electrode Roughness on Dielectric Layer and Capacitance
- Dielectric Layer Uniformity: Rough Ni electrodes can create uneven electric fields in the adjacent BaTiO₃ dielectric layer. Sharp protrusions or irregularities increase localized electric fields, potentially leading to dielectric breakdown.
- Capacitance Stability: Smoother electrode surfaces ensure consistent contact with the dielectric layer, which stabilizes capacitance. In contrast, rough surfaces may cause discontinuities, reducing effective capacitance.
2. Thermal and Mechanical Stress
- Stress from Thermal Mismatch: During sintering, the difference in thermal expansion between Ni electrodes and BaTiO₃ dielectrics induces stress. Rough electrodes amplify these stress points, increasing the likelihood of cracks or defects in the dielectric layer.
- Long-Term Mechanical Integrity: Elevated roughness exacerbates stress concentrations, which can degrade the mechanical integrity of the device over time.
3. Device Lifespan and Insulation Resistance
- Impact on Insulation Resistance: Rough electrodes may intrude more sharply into the dielectric layer, hastening the degradation of insulation resistance under DC electric fields.
- Prolonging Lifespan: Reducing electrode roughness preserves insulation resistance, contributing to a longer operational lifespan for the MLCC.
In conclusion, the shape and smoothness of Ni electrodes are key factors in ensuring uniform electric fields, mechanical stability, and long-term performance in MLCCs.