Understanding Barium Titanate Distribution for MLCC Manufacturing
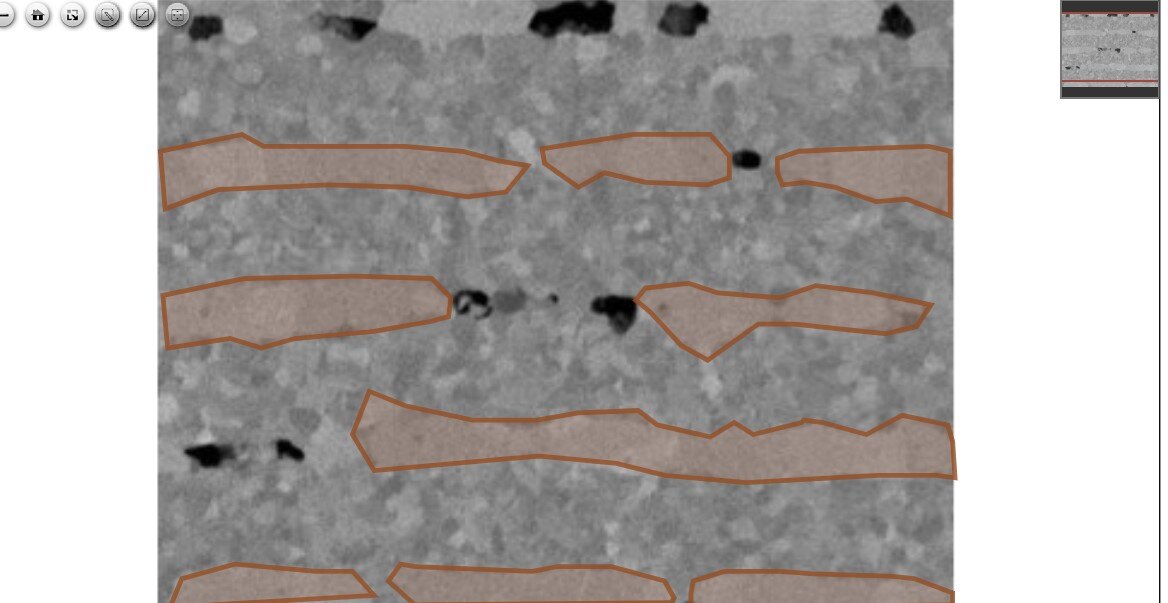
Unlock the secrets of BT particle distribution and its critical role in MLCC manufacturing for enhanced performance and reliability.
The Importance of Barium Titanate Particle Distribution in MLCCs
BT particle distribution plays a crucial role in the manufacturing of multilayer ceramic capacitors (MLCCs), which are essential components in a wide range of electronic devices, from smartphones to automotive systems. These capacitors rely heavily on the dielectric properties of Barium Titanate (BaTiO3) particles to function effectively, as these properties determine the capacitor's ability to store and release electrical energy. Proper distribution of these particles ensures uniformity in the dielectric layer, which is essential for consistent performance across the entire capacitor. This uniformity helps maintain the stability of the electrical field within the capacitor, preventing fluctuations that could lead to performance issues.
Inconsistent BT particle distribution can lead to weak points in the dielectric layer, which are areas where the electrical field is not evenly distributed. These weak points can result in decreased efficiency, as the capacitor may not be able to store as much energy or release it as quickly as needed. Over time, these inefficiencies can lead to potential failure of the capacitor, which can have significant consequences in critical applications, such as in medical devices or aerospace technology. Therefore, understanding and controlling this distribution is vital for producing high-quality MLCCs that meet the rigorous demands of modern technology. Manufacturers must employ precise techniques and advanced technologies to monitor and adjust the distribution of BT particles, ensuring that each capacitor performs reliably and efficiently throughout its lifespan.
Advanced Techniques for Analyzing BT Particle Distribution
Several advanced techniques are employed to analyze BT particle distribution in MLCCs, each offering unique insights and advantages that contribute to a thorough understanding of the material's properties. Particularly, scanning electron microscopy (SEM) is widely used for their exceptional high-resolution imaging capabilities. SEM provides detailed surface images by scanning the sample with a focused beam of electrons, which interact with the atoms in the sample to produce signals that contain information about the sample's surface topography and composition. This allows for a meticulous examination of particle size, shape, and spatial distribution, which is crucial for identifying any irregularities or inconsistencies in the particle arrangement.
TEM, on the other hand, offers even greater resolution by transmitting electrons through an ultra-thin specimen, providing detailed images of the internal structure of the particles. This technique is invaluable for observing the fine details of the particle's internal morphology and for understanding how these details might affect the overall dielectric properties of the MLCCs.
In addition to SEM and TEM, other techniques such as X-ray diffraction (XRD) and energy-dispersive X-ray spectroscopy (EDX) are employed to provide complementary data. XRD is instrumental in determining the crystalline structure of the BT particles, offering insights into the phase composition and crystallographic orientation, which are critical for predicting the material's behavior under different conditions. EDX, often used in conjunction with SEM, provides elemental analysis and chemical characterization of the particles, allowing for the identification of any impurities or compositional variations that could impact the performance of the capacitors.
Together, these methods offer a comprehensive understanding of BT particle distribution, which is essential for optimizing manufacturing processes. By combining the detailed imaging and analytical capabilities of these techniques, manufacturers can ensure that the BT particles are distributed uniformly, thereby enhancing the performance and reliability of the MLCCs. This comprehensive approach not only aids in quality control but also drives innovation in the development of new materials and manufacturing techniques, ultimately leading to more efficient and reliable electronic components.
Impact of BT Particle Distribution on MLCC Performance and Reliability
The distribution of Barium Titanate (BT) particles plays a pivotal role in determining the performance and reliability of multilayer ceramic capacitors (MLCCs). These capacitors are integral components in a myriad of electronic devices, and their efficiency is largely dependent on the uniformity of BT particle distribution. When the distribution is uniform, it ensures that the dielectric properties of the capacitor remain stable, which is crucial for the efficient storage and release of electrical energy. This stability is achieved because a uniform distribution minimizes the risk of creating areas within the dielectric layer where the electric field might be uneven, thereby enhancing the overall performance of the capacitor.
On the other hand, if the distribution of BT particles is uneven, it can lead to the formation of localized stress areas within the dielectric layer. These stress areas are problematic because they can become focal points for electrical stress, which may result in the early failure of the capacitor. Such failures not only reduce the lifespan of the MLCCs but can also lead to significant performance issues in the electronic devices that rely on them. Therefore, it is of utmost importance for manufacturers to implement stringent control measures over the BT particle distribution process. By doing so, they can ensure that each MLCC produced is capable of maintaining its performance over an extended period, thereby guaranteeing the long-term dependability and reliability of these essential components in various high-performance applications.
Understanding Resistance Degradation in BaTiO3 Ceramics and MLCCs
Resistance degradation is a common issue that occurs in Barium Titanate (BaTiO3) ceramics and multilayer ceramic capacitors (MLCCs), often arising from several environmental and operational factors. These factors include moisture penetration, which can lead to the ingress of water molecules into the ceramic material, causing changes in its electrical properties and potentially leading to short circuits. Additionally, exposure to high temperatures can accelerate the degradation process by increasing the mobility of ions within the ceramic, thereby altering its structural integrity and dielectric properties. Electrical stress, which involves the application of high voltage or current, can also contribute to resistance degradation by creating localized heating and mechanical stress within the material, leading to the formation of microcracks or other structural defects.
Understanding the underlying mechanisms of resistance degradation is crucial for developing effective strategies to mitigate these effects. By delving into the specific interactions between environmental factors and the material's microstructure, researchers can identify potential points of failure and devise methods to enhance the material's resilience.
Innovations in MLCC Manufacturing
Advanced deposition techniques are being refined to ensure that these nanostructured particles are applied with the utmost accuracy, minimizing defects and maximizing the efficiency of the dielectric layers. These techniques involve sophisticated processes that can precisely control the thickness and composition of the layers, leading to capacitors that are not only more reliable but also capable of operating under more demanding conditions.
In addition to these material and process innovations, the integration of artificial intelligence (AI) and machine learning (ML) into manufacturing processes is poised to transform the industry further. AI and ML technologies can analyze vast amounts of data in high speed, enabling manufacturers to optimize production processes dynamically.